Les constructeurs misent sur l’écoconception afin d’atteindre des taux de valorisabilité et de recyclabilité toujours plus élevés. Certains mettent aussi en place une économie circulaire pour récupérer et reconditionner les composants les plus nobles. Cependant, ces industriels ne prennent pas en charge le recyclage du matériel roulant en fin de vie. Ils commencent néanmoins à s’y préparer dans la perspective d’un élargissement de la responsabilité élargie des producteurs (REP) aux constructeurs de véhicules lourds inscrite dans une proposition de Règlement du Parlement européen et du conseil déposée en juillet 2023… et d’une demande naissante des AOM.
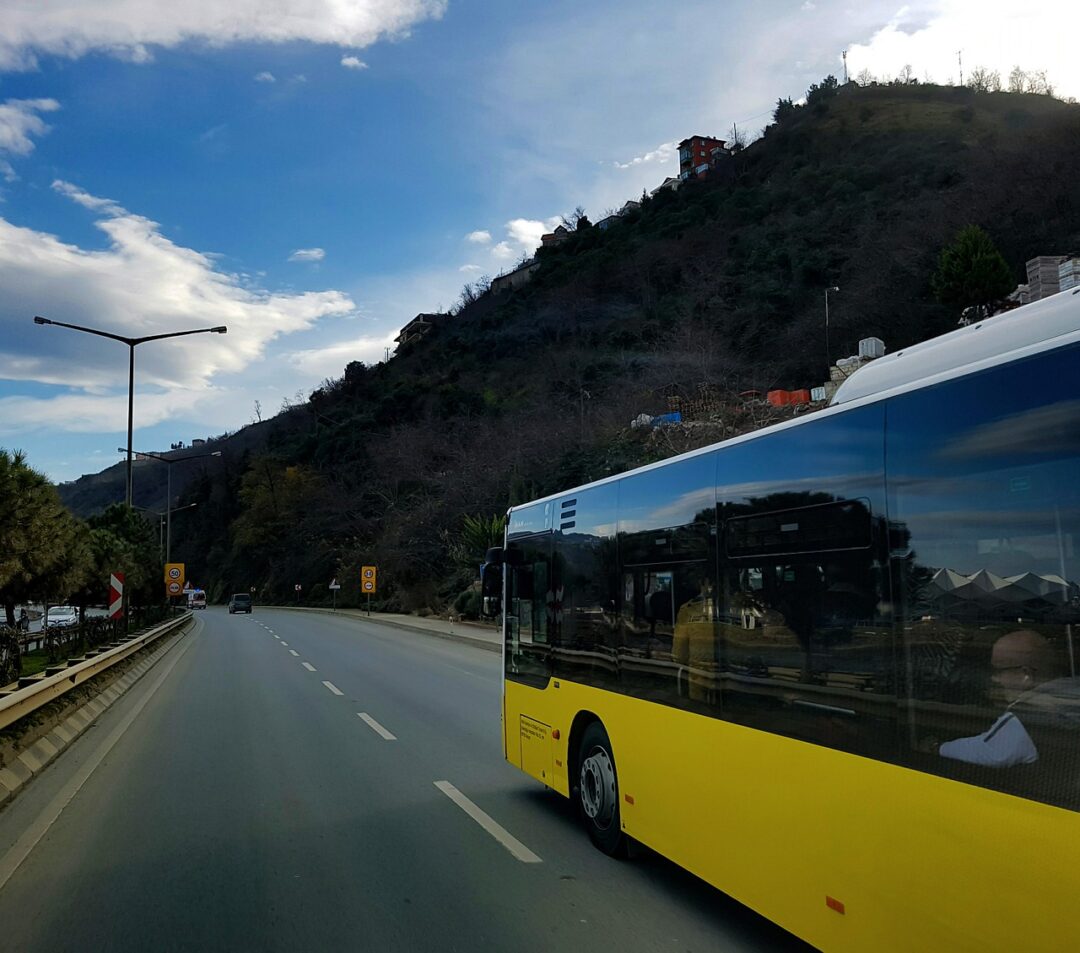
Ecoconception
« La performance comme le comportement en fin de vie des solutions ferroviaires, dépendent fortement de la phase de conception des produits », souligne Véronique ANDRIÈS, vice-présidente RSE et développement durable d’Alstom. L’industriel a fait de l’innovation dans l’écoconception et la durabilité de son matériel roulant, « une de ses priorités », assure Véronique ANDRIÈS. Le Groupe a commencé à travailler sur ces sujets dès les années 90 et a notamment participé, en 1996, au co-développement du logiciel d’analyse du cycle de vie (ACV) et d’écoconception EIME. Alstom identifie alors plusieurs problématiques qui vont gêner le recyclage comme des incompatibilités entre des matériaux et des composants, et des difficultés à séparer facilement et rapidement des matériaux. « Plus ce temps est important, plus il est coûteux, et plus cela dissuade de tenter la séparation. Le taux de recyclage diminue alors automatiquement », explique Véronique ANDRIÈS.
Ces problématiques ont été intégrées, à partir de 2004, dans le cahier des charges des nouveaux trains conçus par les équipes R&D d’Alstom : en 2023, 65 % des nouvelles solutions étaient éco-conçues, l’industriel affichant un objectif d’atteindre 100% d’ici à 2025. « Cette démarche induit une cascade de spécifications pour nos fournisseurs. C’est ainsi que petit à petit la chaîne de valeur s’organise pour intégrer ces principes qui expliquent qu’aujourd’hui, nous obtenons des taux de recyclabilité qui sont très élevés sur nos trains », souligne Véronique ANDRIÈS.
Des fournisseurs tenus de signer la Charte éthique et développement durable d’Alstom pour travailler avec l’industriel et qui doivent remplir ses exigences : « Chaque composant (morceau du train) reçoit sa liste de courses qui sert à la consultation des fournisseurs. Nous sélectionnons celui qui répond le mieux aux performances technico-économiques recherchées », indique Véronique ANDRIÈS. Par exemple, des sièges plus légers participent à la réduction de la consommation d’énergie d’un train. « Il est important de souligner que c’est une démarche holistique, car elle adresse à la fois des enjeux de décarbonation et de ressources, et de manière générale l’ensemble des impacts environnementaux que nos solutions peuvent avoir sur le cycle de vie », insiste Véronique ANDRIÈS.
Les fabricants de bus et d’autocars travaillent également sur l’écoconception. Premier objectif ? Réduire le poids du véhicule, facteur principal de réduction de la consommation d’énergie. Une stratégie qui les conduit à utiliser de nouveaux composants à l’instar du néerlandais Ebusco, constructeur de bus électriques à batteries depuis 2012.
L’Ebusco 3.0, homologué en 2021, s’inspire des matériaux composites utilisés dans l’aéronautique : la structure acier est remplacée par une structure en fibre de carbone, l’assemblage ne se fait plus par rivetage, mais par collage. Les panneaux sont en fibre de verre. Résultat, une réduction de 30% du poids de ses bus, qui se retrouve quasiment 1 pour 1 dans la consommation d’énergie, selon Louis-René CHABANNES, directeur de projets Ebusco France Sales. Surtout, avec des matériaux moins sujets à la corrosion, le constructeur annonce une durée de vie fonctionnelle de ses bus jusqu’à 25 ans, contre généralement une quinzaine d’années pour ceux conçus en acier. Les réparations sont également moins onéreuses, selon Ebusco, car il n’est pas nécessaire de changer l’ensemble du composant en fibre de verre ou de carbone : il suffit d’utiliser un patch pour réparer la partie endommagée. De même, les bas de caisse sont protégés par des panneaux en plastiques aisément remplaçables. Au final, cette écoconception permet à Ebusco d’annoncer des taux de valorisation proches de 90% durant son cycle de vie, et des taux de recyclabilité supérieurs à 80%.
Dans leurs bureaux de Vénissieux près de Lyon, les équipes d’Iveco Bus chargées de l’écoconception cherchent aussi le meilleur compromis entre la réduction de poids et la durabilité pour des véhicules qui parcourent 800 000 km voire 1,5 million pour les autocars. Depuis 2022, Iveco Bus réalise une analyse du cycle de vie (ACV) de son matériel roulant. « L’ACV est demandée par les collectivités dans le cahier des charges. Nous visons également à offrir des solutions optimisées en termes de coût total de possession (TCO), un élément clé dans le processus décisionnel de nos clients », explique Jean-Marc BOUCHERET, Sustainable Mobility Manager d’Iveco Bus. Le groupe italien, qui fait partie du Dow Jones sustainability index et a obtenu la médaille d’or lors de sa certification Ecovadis, affiche des taux de recyclabilité de plus de 90% et de valorisabilité de plus de 95% pour ses modèles selon la norme ISO 22628.
Irizar se concentre également sur la baisse du poids de ses véhicules. Le constructeur espagnol annonce aussi avoir changé ses méthodes de fabrication de ses bus électriques pour mettre l’accent sur la démontabilité et la recyclabilité des composants, notamment en changeant le système traditionnel de soudure par un nouveau système de vissage modulaire de la structure en aluminium. Ainsi, Irizar affiche des taux de recyclabilité et de récupérabilité de ses autobus électriques supérieurs à 90 % selon la norme ISO 22628. Le taux de recyclabilité des composants et matériaux qui composent l’autobus modèle Irizar ie bus est de 98,92%, selon les résultats d’une analyse réalisée en collaboration avec iHobe, société publique de gestion environnementale du gouvernement basque.
Irizar s’appuie sur les méthodologies d’analyse du cycle de vie (ACV) et d’établissement des règles de catégorie de produits pour évaluer l’impact environnemental de l’ensemble de ses modèles – à combustion, hybrides et électriques : en 2019, Irizar est ainsi devenue la première entreprise du secteur au niveau mondial à obtenir une Déclaration environnementale de produit (DEP) pour son modèle Irizar i4 intégral. Une certification qui lui permet de connaître sa performance environnementale, de l’améliorer au fil du temps et de la comparer à d’autres produits de la même catégorie. Enfin, cette DEP est de plus en plus demandée aujourd’hui dans les appels d’offres, selon Irizar.
Reconditionnement
La loi anti-gaspillage pour une économie circulaire adoptée début 2020 encourage les industriels à réutiliser les matériaux et à prolonger la durée de vie de leurs produits.
Iveco Bus s’est donné pour objectif que 15% du chiffre d’affaires net des pièces détachées soit généré par des composants remanufacturés d’ici à 2026, soit un quasi-doublement par rapport à 2023 (7,7% au niveau mondial). L’idée est de récupérer les matériaux qui ont une valeur marchande – moteur, transmission, organes liés aux essieux… Son usine de reconditionnement de moteurs, située en Bourgogne, récupère ces pièces nobles pour les reconditionner et les remettre sur le marché avec sa garantie constructeur. En 2023, Iveco Bus a ainsi récupéré 45% des composants de moteurs sélectionnés et a un objectif à moyen et long terme de 80%. « Cela permet à nos clients d’utiliser des pièces moins onéreuses que des pièces neuves, et de réduire les coûts de maintenance en seconde partie de vie du véhicule. Une pièce reconditionnée n’en demeure pas moins une pièce d’origine qui respecte les exigences de qualité et de sécurité constructeur », souligne Jean-Marc BOUCHERET. Ceux-ci économisent, en moyenne, 30% sur le prix catalogue grâce à ces pièces reconditionnées, selon Iveco Bus.
A fin 2023, 30% des composants récupérables des pièces détachées vendues dans le monde par Iveco Bus, ont été collectés pour être réutilisés, reconditionnés ou recyclés. L’industriel a désormais pour ambition de parvenir à 100% de récupération des composants provenant des pièces détachées vendues retournées à l’entreprise d’ici à 2030. « Pour atteindre cet objectif, nous devons créer un réseau capillaire avec nos centres de maintenance pour que ces composants ne soient pas perdus. Nous devons également mettre en place un flux logistique inverse pour récupérer ces pièces et les acheminer dans des usines dédiées à leur reconditionnement », explique Jean-Marc BOUCHERET.
De son côté, Mercedes-Benz a lancé OMNIplus, une marque de service dédiée à l’achat de pièces de rechange reconditionnées pour ses bus diesel et électriques. L’offre comprend près d’une trentaine d’organes et de composants : du moteur à la simple vis. Mercedes-Benz explique que les pièces d’origine reconditionnées sont soumises au préalable à « un processus de reconditionnement approfondi » : « À la fin de ce processus, le résultat est une pièce d’origine reconditionnée de qualité première qui correspond au niveau de standard élevé OMNIplus en matière de précision de montage, d’état technique, de performance, de sécurité et de garantie », revendique le constructeur allemand.
Pour ses modèles plus anciens en acier, Ebusco va notamment travailler avec son fournisseur finlandais qui incorpore déjà de l’acier recyclé : « L’idée est qu’il reprenne les châssis qu’il nous a fournis. Cette démarche n’a pas encore été mise en œuvre, car nos bus sont trop récents », explique Louis-René CHABANNES. S’agissant du dernier modèle, l’Ebusco 3.0 en fibre de verre et de carbone, le constructeur a passé des accords avec des universités pour concentrer la Recherche sur le réemploi de ces matériaux composites pour des matériaux de construction, par exemple. Les expérimentations, à ce stade, sont limitées à une petite échelle.
Seconde vie
Avant d’envisager le recyclage, certains composants d’un véhicule peuvent être utilisés pour d’autres applications. C’est le cas des batteries dont le Règlement (UE) 2023/1542, encourage leur réemploi et réaffectation en seconde vie. Lorsque leurs performances tombent en dessous du minimum garanti par les constructeurs (80%), elles sont retirées des bus, mais peuvent encore servir pour intégrer des systèmes de stockage d’énergie stationnaires, mais aussi mobiles. Cette énergie stockée pourra, par exemple, servir à alimenter des blocs électrogènes et des systèmes de recharge de bus au dépôt. Les constructeurs commencent tout juste à proposer ce type de solutions dans la mesure où ces batteries étant encore en service, il est trop tôt pour mettre en œuvre leur réemploi.
Ainsi, Mercedes Benz travaille sur une seconde vie des batteries NMC (Nickel Manganèse Cobalt) de ses bus eCitaro : le constructeur imagine des solutions de stockage stationnaires, qui pourraient, par exemple, récupérer l’énergie issue de l’exploitation de tramways afin de s’en servir pour recharger des bus électriques. Tout l’enjeu consiste à absorber les pics de charge dans la consommation ou dans la production d’électricité grâce à la technique du peak shaving qui consiste à réduire la consommation d’électricité pendant les heures de pointe.
« L’intérêt pour nos clients est de stocker de l’énergie quand celle-ci n’est pas chère pour la réinjecter plus tard pour la recharge des bus ou d’utiliser cette énergie stockée lorsque que le besoin de recharge est particulièrement important à un instant T : au final, cela permet de réduire la facture d’électricité », souligne Jean-Marc BOUCHERET. Par exemple, Iveco Bus a lancé un projet pilote avec la ville de Maribor en Slovénie qui s’inscrit dans le cadre du programme d’économie circulaire CE4CE et qui concerne des batteries FPT, marque d’Iveco Group.
De son côté, Ebusco a lancé Ebusco Energy, une branche d’activité dédiée à la seconde vie des batteries qui équipent ses bus : le constructeur propose des containers de batteries qui permettent de stocker l’énergie produite par des sources d’électricité intermittente comme l’éolien et le photovoltaïque, par exemple. Le fabricant conçoit également des containers mobiles afin de permettre une électrification flexible et temporaire d’un site comme des chantiers et des festivals. Ebusco investit aussi le secteur maritime : le Néerlandais a ainsi passé un accord avec Oechies Elektrotechniek, une entreprise qui exploite des barges aux Pays-Bas pour alimenter ses bateaux à hydrogène avec ses containers mobiles.
En 2019, Irizar a conclu un accord avec Ibil, entreprise spécialisée dans la technologie pour la recharge de véhicules électriques en Espagne et au Portugal. Ses batteries servent en seconde vie comme élément de stockage d’énergie dans des infrastructures de recharge qu’Ibil développe et déploie notamment pour les stations-services de Repsol. La première a été mise en service en 2021. Cinq stations à ce jour sont équipées. Cette solution présente l’avantage d’installer des points de recharge de 50 kW dans des endroits qui ne disposent pas d’une puissance électrique suffisante, ou dont le coût d’investissement dans le réseau rend d’autres alternatives irréalisables, explique Irizar dans son mémoire de durabilité 2023.
Recyclage
Le Règlement européen 2023/1542 impose aussi une gestion responsable des batteries en fin de vie afin de minimiser leur impact environnemental. Les producteurs de batteries sont responsables de la collecte, du traitement et du recyclage des batteries mises sur le marché, en vertu des principes de la responsabilité élargie des producteurs (REP). Cela inclut des obligations financières et organisationnelles pour garantir une gestion durable des batteries en fin de vie.
Ainsi, pour le recyclage de ses batteries lithium-ion, Iveco Group a passé un accord, en janvier 2024, avec BASF qui possède un site dédié en Allemagne.
Ebusco va travailler avec un groupement d’industriels français qui doit ouvrir une usine dans le Grand port maritime de Dunkerque à partir de 2025. Une grande partie des composants utilisés peut être récupérée – carbonate de lithium, hydroxyde de lithium, nickel, cobalt, manganèse, cuivre, aluminium.
D’après Mercedes-Benz, il est possible d’atteindre des quotas de plus de 90% selon les matières considérées. Ces dernières sont ensuite réutilisées pour la production de nouvelles batteries.
En revanche, cette REP issue de la Directive 2008/98/CE relative aux déchets, ne s’applique pas au recyclage des véhicules utilitaires lourds comme c’est le cas dans l’automobile. En clair, les constructeurs ne sont pas tenus de financer la collecte, le traitement et le recyclage des véhicules hors d’usage. Il n’existe donc pas de filière établie pour le démantèlement, la dépollution et la récupération des matériaux issus de ces véhicules lourds. A la fin de l’exploitation des bus sur un réseau de transport par exemple, le matériel roulant, propriété de l’AOM, n’est pas repris par les constructeurs. Il appartient au client, soit de faire don de ce matériel à un pays émergent, soit de l’adresser à un ferrailleur.
Cependant, une proposition de Règlement du Parlement européen et du conseil datée de juillet 2023 prévoit que les constructeurs de véhicules utilitaires lourds aient les mêmes obligations de recyclage que le secteur automobile, qu’ils soient soumis aux mêmes exigences liées à la REP et qu’ils doivent fournir des informations sur l’extraction et le remplacement des pièces, composants et matériaux de ces véhicules hors d’usage afin de faciliter leur traitement. Iveco anticipe que cette proposition de règlement entrera en vigueur vers 2030 : « Nous portons une attention particulière sur le life cycle thinking : cela inclut la conception, la production, les usages et la fin de vie. La production et notre activité sont imaginées dans cet esprit, assure Jean-Marc BOUCHERET. Reste qu’il faudra mettre en place une filière de revalorisation de ces matériaux… »
En outre, toutes les AOM n’attendent que la REP devienne obligatoire pour l’imposer aux industriels : « Faire porter sur les fabricants, la responsabilité de la fin de vie du matériel roulant, est une idée qui fait son chemin, explique Véronique ANDRIÈS d’Alstom. Aujourd’hui, deux cas de figure se présentent : lors de la vente d’un nouveau train, le client souhaite que nous gérions sa fin de vie 30-40 ans plus tard ; d’autres demandent dans les appels d’offres que le constructeur reprenne leur ancienne flotte quand nous leur en vendons une nouvelle. » Même si cette seconde option n’est pas encore généralisée, l’industriel récupère alors des trains conçus voici 30-40 ans qui n’ont pas été optimisés pour la fin de vie : en clair, le nombre de composants à récupérer est bien moindre qu’aujourd’hui.
« Cette phase de gestion de la fin de vie n’est évidemment pas le cœur de métier d’Alstom, mais cela fait partie des services que nous souhaitons proposer à nos clients, explique Véronique ANDRIÈS. Nous chiffrons alors les coûts liés à la reprise et au démantèlement des rames. Nous nous associons à des partenaires qui vont nous facturer certaines étapes… Cette prestation est vendue à l’acheteur du matériel roulant. Son prix dépend de ce qui peut être valorisé. »
Ainsi, plusieurs industriels comme Alstom mettent d’ores et déjà à la disposition de ces prestataires des manuels de fin de vie : « Le client veut savoir quels sont les composants qui ont de la valeur, comment il faut les démonter et quelles précautions il faut prendre pour les démonter… », explique Véronique ANDRIÈS. Le Groupe vend sa connaissance du matériel roulant : lui seul sait précisément comment sont assemblés les composants, où ils se trouvent, et est capable de déterminer les besoins de réemploi de certaines pièces. Alstom travaille d’ailleurs sur toutes les possibilités de mise en œuvre d’une économie circulaire… »